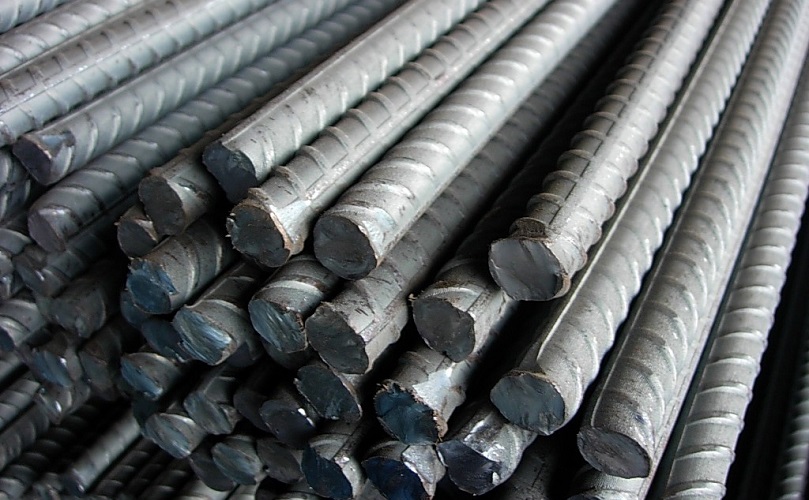
Rebar
What is rebar?
Rebar or reinforcement is a steel used in concrete to compensate for its low tensile strength. Steel used for this purpose in reinforced concrete structures is in the form of wires or rebars and is called rebar steel. Of course, in certain cases, construction steel such as studs or cans is also used to arm concrete.
In different countries, rebar steel is produced with different standards and in each standard there is a certain classification in relation to the mechanical properties of steels. In Iran, the majority of Armature steels produced by Esfahan Steel Mill comply with Russian standard.
In terms of the variety of rebar diameters, manufacturers' standards also vary. In the Russian system used in Isfahan steel mills, rebars up to 40 mm in diameter are made
Types of rebar and their mechanical specifications:
The most rebar used in the concrete and concrete industry is characterized by ordinary steel, which is classified, produced and consumed in Iran as follows. Of course, this category is according to the Russian standard which is common in Iran.
1- Soft rebar without tread (A1)
This rebar with current stress of 2300 kg/cm2 and stress of 3800 kg/cm2 and relative plastic deformation (at the time of rupture) is 25% known as soft rebar and is mainly smooth and treadless. This rebar is suitable for forging and deformation and welding operations on it and is generally known as a ductile rebar.
2- Semi-hard rebar with simple tread (A2)
This type of rebar with current stress of 3000 kg/cm2 and stress of 5000 kg/cm2 and relative plastic deformation (at the time of rupture) 19% as semi-arid rebar (wet) This rebar is suitable for construction operations, especially raw materials, and welding operations are possible if forced, which is recommended in case of compulsion. The possibility of welding it should be avoided.
3- Hard rebar with intricate tread (A3)
This rebar with current stress of 4000 kg/cm2 and stress of 6000 kg/cm2 and relative plastic deformation (at the time of rupture) 14% as dry rebar (crisp) It is suitable for industrial and construction civil operations which are ribbed and mainly treading and are strictly not suitable for forging and many deformations with fast angles and also welding operations are not allowed on it in any way.
4- Hard rebar with intricate tread (A4)
They have a spindly tread. According to standard no. 3132 of The National Standards Organization of Iran, A4 rebar or tread bars 520 and 500 are compound ribbed. In this way, dooky-shaped transverse treads on both sides of the longitudinal tread and in the form of four half-helixes are seven-eight and at an angle of 35 degrees to 75 degrees. Guarantees a minimum tensile strength of 520 MPa and a ductility of at least 18% for this grade of its products.
The use of A4 rebar with yield stress of 500 and 520 MPa, respectively, are referred to as tread bars 500 and 520 aj, in the design and construction of all types of construction structures (does not include non-construction structures) reinforced concrete, except for special shear walls and special bending frames, if the following conditions are adopted.
– The rebar has spindle-shaped transverse treads on both sides of the longitudinal tread.
– The ductility of the rebar is at least as high as expected for the A3 rebar, so that its relative length increase is at least 16% in a length equal to 5 times the diameter.
– Do not use high carbon ingots in the production of rebar. The method of producing rebar is thermex technology and the carbon equivalent (CE) of rebar is up to 0.5.
– The rebar manufacturer has obtained the certificate of national standard organization for the production of 500 tread bars and 520 aj and has carved the factory and the rebar category on it.
Appearance of A2 and A3 rebars
In the sought-after design, longituditudre rebar A3 and transverse rebar A2 are used. One way to identify the shape is tread. In A3 bars, the treads are multiplied, but in A2 they are single. In A2 bars, the treads are parallel, but in A3 bars the treads are seven and eight.
Types of rebars based on the current standard and analysis
Simple Rebar 240 (Simple Rebar)
Ribbed rebar 340 (spiral ribbed rebar) or (uniform)
Ribbed rebar 350 (spiral ribbed rebar) or (uniform)
Ribbed rebar 400 (treadmill rebar) or (uniform)
Ribbed rebar 420 (twil ribbed rebar) or (uniform)
Ribbed rebar 500 (compound ribbed rebar)
Ribbed rebar 520 (compound ribbed rebar)
Currently, all market bars are subject to such a standard.
When you hear the name of the A2 rebar, know that it means the tread 340 rebar, and the A3 rebar is the tread 400 rebar. Only names remain constant, but their analysis and standard are quite different.
Method of detection of tread rebar 340 and tread rebar 400
At tread 340, the treads are spiral at an angle of 45 degrees. At 400 tread angles, the treads are 45 degrees, but if you look at the rebar from the front, the treads are twilly (seven and eight).
Mechanical properties of rebars – strain and tension and bending tests
Tension of submission
The maximum force that enters the rebar and the rebar does not suffer permanent deformation. If the force value increases, the rebar will not return to its original mood and will permanently deform. Reversibility is called elasticity and irreversible properties are called plastic properties. In designs, the criterion for choosing rebar is the amount of yield stress
That's why, because of this very important property, the amount of yield stress is in the naming of rebars. In tread rebar 340, the minimum yield stress of this rebar is 340 MPa.
Tensile strength
Tensile strength is the most tensile force that the object tolerates before failure. Its unit is pounds per square inch. The tensile strength of rebars can be enhanced by operations such as alloying, cooling, or heat treatment. Similar expressions used for tensile strength include tensy strength– tensie strength. In the tensile test and relative length increase, the degree of flexibility or fragility of the rebar is determined.
Types of rebar application (reinforcement) in concrete
Rebars are used in different forms in reinforced concrete members, which are usually more accurate in structural maps. Different applications are listed below.
What is Rebar Rasta
To increase the tensile strength of concrete
What is Hamut Rebar
To prevent the protrusion of longitudinal armatures due to buckling and tolerance of shear forces and preventing crack expansion.
What is Dragonfly Rebar
To strengthen the shear strength of the hamuts and the complete connection between longitudinal mills and hamut
What is Rebar Vault
To place two horizontal sequential networks with a certain distance inside the mold (in floor concrete and foundation)
What is Rebar Rekabi
To keep longitudinal or vertical armatures in concrete walls and slabs (in the form of letter u) or between two armature tablecloths (network meshing)
What is Edka Rebar
Negative anchors in beam support and for shear forces tolerance
Rebar foundations
In practice, the rebars are placed in a grid on the floor of the foundation (including the distance of the concrete coating) to create more adhesion and more suitable transfer of force between steel and concrete on the sides of the foundation, the grid rebar is formed with a bend of 90 degrees to a certain length.
Due to the amount of load and depth of foundation of the rebar system in them, it can be in the form of lower networks or a combination of inferior and upper networks.
To maintain a suitable distance between the two networks, vault (rebar bent as a support) is used.
Rebar Usage
Mortar walls and stone structures are almost similar to concrete in terms of specifications and have poor tolerance to tensile stresses. Some standard pieces of stone such as bricks and blocks are designed to strengthen them against tensile stresses by placing rebar in these holes.
although any material with high tensile strength can be used as a reinforcing agent to strengthen the tensile strength of concrete, and due to the special commonality between steel and concrete, it has caused more steel to be used to make reinforcement rebars.
The temperature expansion coefficient in concrete and steel is the commonality between the two and the proximity of this coefficient prevents the occurrence of additional internal stresses in the concrete structure under different temperature conditions, which prevents the early destruction of concrete.
What is alloyed rebar and thermex (cooling and return under control)?
Rebar production processes in developed countries of the world are in different ways. In the world's most prestigious standards, according to the climatic conditions of each country, production processes are completely clear and controlled according to different parameters:
1- In Japan, which is earthquake-prone in terms of climatic conditions, its national standard JIS defines chemical analysis in accordance with the production process (by alloy method) and makes no mention of the production process through heat treatment (thermex) and in other words, the use of thermex bars in that country is not recommended.
2- In European countries that are safe in terms of earthquakes and have a much lower risk of earthquake than Japan, the thermex method (heat treatment) is considered and chemical analysis is considered according to the process of armature production by the above method,
3- In the National Standard of Iran no. 3132, which is derived from several reference standards (European EN, DIN, and Japan JIS, USAASTM and ISO), both methods are considered, but due to the high security factor of consumption in paragraph 13 of the standard (markup) it is clearly obliged manufacturers to inform the consumer in terms of the process of rebar production.
In this way, it should be carved on the attached plaque as a characteristic sign indicating the production by the thermex method and the sections of the branches of this product should be painted in a defined color and also in the technical certificate such as the production process by cooling and returning under control.
According to the national standard of Iran, welding operations on these types of rebars are not allowed.
It should be noted that in the alloying method, the steel needed to produce the desired reinforcement is made in the steelmaking process and through the addition of ferroalloys, and the ingot produced in the rolling process becomes the desired form and then cools in a free and gradual environment.
In this case, the produced armature from the outer surface to its center has the same mechanical properties and chemical properties and in the event of earthquake and pressure, it has a uniform and more suitable resistance.
But for the rebar produced by the thermex method, the steel ingot used has a lower chemical analysis class and to achieve the required resistance according to the standard, the produced rebar which has a high temperature passes through the water pipes and cools the outer surface at once. In this case, the level of rebar to a certain depth has a higher resistance (e.g. 400), but the armature brain will have a lower resistance (e.g. about 340).
Therefore, the use of this type of reinforcement in pressure structures and earthquake-prone areas should be taken precautions and double accuracy should be applied in its calculations. The cost of alloyed rebars is higher than thermexi.
Standard types of rebar and their differences
The strength of concrete is tremendous. It takes a lot of force to crush the concrete. However, concrete has a relatively weak tensile capability and less force is needed to leave the concrete by bending or twisting than we want to crush it directly. Reinforcing rod or reinforcement is used to increase the tensile strength of concrete.
Reinforcements are available in different lengths and diameters, but there are only 6 common types:
European Rebar:
The strong point of European rebar is its price. Basically, it is produced from manganese, and has the lowest resistance among armatures in terms of bending. The use of this type of reinforcement is usually not recommended in earthquake-prone spaces and projects that require an important correct structure.
Carbon steel rebar:
Black rebar is used in any project except for a few exceptions. The biggest weakness of the black armature is its rust. When he calls, he leaves the concrete around him and breaks. In situations where moisture and water may be exposed, there are better choices than black rebar. However, due to its value ratio to the tensile strength of black rebar is the best.
Epoxy coating:
Epoxy coated rebar is the same as the epoxy-coated black armature. It has the same texture strength, but is 70 to 1,700 times more resistant to rust.
Galvanized rebar:
Only forty times more resistant to rust than black rebar, but it is much harder to damage the galvanized rebar veneer. For this reason, epoxy coating rebar is more valuable. Although it is approximately 40% more expensive than epoxy coating.
Fiberglass Rebar:
Fiberglass is a compound similar to carbon fiber. As a result, bending is not allowed when using fiberglass. However it doesn't ring. Due to this, fiberglass is an unparalleled concrete reinforcing rod. While each half kilogram is 10 times more expensive than epoxy rebar, it's incredibly light. So considering the length of the price, it's almost twice as long.
Stainless Steel:
Stainless steel rebar is the most expensive reinforcing rod available, about 8 times the price of epoxy armature. This is the best armature for most projects. However, the use of stainless steel in all place except for very unique conditions is usually not useful. But for people who have reason to use it, stainless steel rebar is 1,500 times higher than black rebar to rust. Compared to others, it is much more resistant to damage than stainless and rust-resistant rebar samples.
Proper maintenance of rebar
• When the construction company receives the rebars, they must be placed on wooden pallets or a non-metallic surface. Storing them in these conditions prevents rust over time by groundwater.
• When storing rebar on wooden pallets or a non-metallic surface, be sure to cover them with a waterproof coating.
• Place heavy blocks on the cover corners to protect the rebar well. Prolonged placement of them in an open environment can cause rust and lower its productivity level.
Specifications and rebar identification number
During the hot rolling process and using different types of steel, round mill is produced. Often, rebars are made of newly produced steel. But iron waste is sometimes used to produce rebar. Using specific identification information that rebars have, their specifications can be determined.
The following information is the standard set by the American Association for Testing and Materials for each rebar:
• For example, the letter N means that the round mill is made of new steel and the letter W means that the rebar is made of casting steel.
• Rebar grade ID, which can be 60 or 75 in the English measurement system and can be 420 or 520 in the metric metering system. This identifier represents the strength of the rebar surrender.
• Abbreviation sign of rebar manufacturer. This sign is often in the form of the first letter of the manufacturer's name.
Low strength bars are identified only by three indications that represent the rolling used in the manufacture, size of the rebar and the type of steel used. In high strength steel bars, continuous lines are used to determine the degree of rebar strength. Two continuous parallel lines indicate that the rebar is built under rolling at 75,000 pounds per square inch, and one line is a sign of rebar production under rolling at 60,000 pounds per square inch.