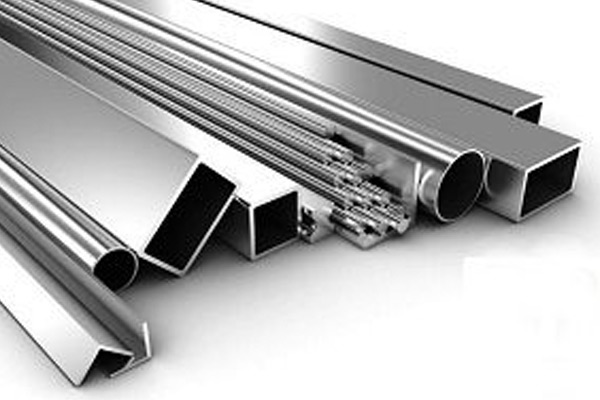
Profile
What is a profile?
PROFILE literally means a fixed cross section and a long length that is used in construction and machine building. In this article, we want to acquaint you with the concepts of profile, its application and production method.
Profile types:
A: Open profiles include beams, belts, corners, studs, rebars.
B: The closed profile includes pipes and cans.
Profile application:
Profiles have many uses in construction, industry and road construction, but it is mostly used in the construction of iron doors and windows.
The profiles are square and rectangular, with small sections used for metal railings for doors and windows, stairwells, factory wall railings, sidewalks, and streets, but larger sections of the profiles are known as columns. Are used in the construction of columns and steel structures.
Other uses of profiles:
In the automotive industry
In the construction of table and chair bases
Type z to cover the roof of sheds
Construction of large iron door frames using corner profiles
Construction of shop shutters using stud profiles
How to produce a type of square profile:
Production of profiles and construction cans is done in two direct and indirect methods (the same production of pipes and conversion into the final form), each of which has advantages and disadvantages.
Direct production method:
In the direct production method, the strip is gradually formed by passing through the upper and lower molds (with actuators) and next to the wastes, which the designer has done by performing calculations in terms of the amount of force and angles of the desired shape, which he designed by distribution in each gate. After welding the two edges of the sheet by frequency welds, it finally forms a complete shape in the sizing part.
The profile produced by the force exerted by the molds and the welding heat is not completely straight and is modified by bending, twisting, twisting and buckling by applying force again. The profile under production is cut by an automatic saw at intervals of 66 meters and packed in a certain number and after installing the specifications card and confirming the quality control, it is transferred to the product warehouse.
Advantages and disadvantages:
The profile produced by direct method has a higher quality and has sharp angles, precise dimensions and fixed welding line in the upper wall and has a small surface curvature.
In this method, due to the sharpness of the corners and the difference in diameter of different points of the molds and different linear velocities, the depreciation of the molds is more. Also, in terms of machining and heat treatment, more precision is required. On the other hand, more air space between the inductor and the profile and ferrite will reduce the production speed and will have a lower speed and lower efficiency than the indirect method.
Indirect production method:
In this method, the profile is first turned into a pipe in the main rolling machine according to the above steps and one of the three bending methods, and after welding the two edges, in the sizing and torsion section due to high, low and side pressures, this pipe Various shapes are converted or more complete in the sizing and twisting part of the pipe and the final product is produced and packaged after cutting.
Advantages and disadvantages
In this method, the initial part of the machine (including Forming and Finishing) is converted into one of the three ways of edge shaping, central shaping or shaping through the real radius and according to the designer's opinion and machine conditions, in the sizing section It is converted to the desired shape, which is called Online method, or after the tube is complete and cut in this round, deformation is performed in other devices.
In this method, because you can make a pipe in the forming part and change at least a few molds in the sizing part or take it to other non-welded devices, several types of profiles can be prepared. Having variety is possible with a minimum of pipe making machine. In addition, because the air distance between the inductor and the pipe can be kept to a minimum and the selected diameter can be as high as possible, the maximum power of the welding machine can be used and the production speed will be higher than the direct method.
Curved molds are easier to make with the machine and in heat treatment the probability of breaking is much less due to the lack of sharp corners, but in terms of quality, the corners are rounder and the size of the sides, welding line and surface curvature are lower than the method. It will be straightforward.If the production of the pipe is only for the supply of gas or water pipe, the diameter of the pipe in the welding section is about half a millimeter larger than the final diameter, and this amount of excess pipe diameter increases with the linear velocity created by increasing the diameter of the molds in each gate. They reduce 0.5 to 0.2 mm in sizing and practically stretch and round the pipe.
The produced pipe can be tested before cutting by non-destructive eddy current test (magnetic field) or after cutting offline test, and then after pleating, the hydrostatic test can be performed up to a pressure of about 70 times for 5 minutes. Seconds and after confirming and printing the necessary specifications on the tubes in a hexagonal package and marketed. This method is also used for cans, beams, angles and studs.
Application of various profiles
Square and rectangular profiles with small sections are used as metal railings for doors and windows of houses, side stairs, as well as fencing around factory walls and enclosed lands, and sidewalk and street railings.
Square and rectangular profiles (cans) with larger sections, which are known as columns, have many uses in industry and construction. These profiles, which are made in square sections and their thickness is from 1.5 to 8 mm can be Used in the construction of columns and metal structures of buildings. Also, if these profiles are made with reliable physical specifications, they can be used in the construction of trailer chassis and tankers.
Square and rectangular can profiles are also used in the automotive industry.
Square can profiles are also used to make table and chair bases.
Z-shaped profiles are often used to cover the roofs of sheds.
Corner and stud profiles are also produced by cold rolling method. Corner profiles can be used to make large iron door frames and a variety of metal molds used in machinery. Small studs are used in cases such as shop shutters.
List of factories producing angles and studs in Iran
Iran has many gutter factories, including the following:
There are Nab Tabirir, Mahan, Arian Foolad, Yazd, Tehran Steel, Abhar, Zanjan, Zohourian Mashhad, Shokfteh Mashhad Industrial Group, Milad Yazd Rolling Industries, Spiral, Isfahan Sepahan Steel, Manzoomeh, Kuhpayeh Steel Industries, etc. , Nab Tabriz factory has the highest quality.