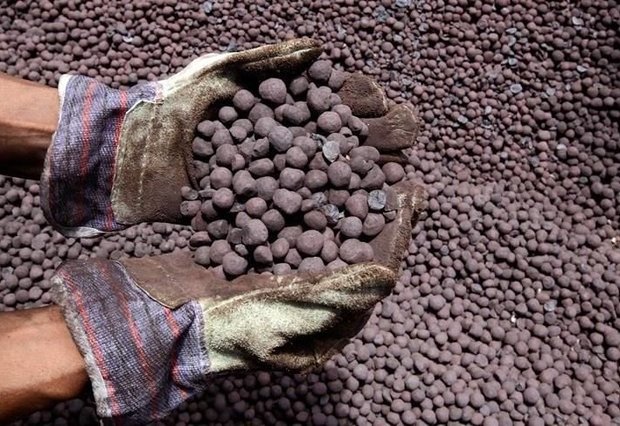
Sponge Iron
What is sponge iron and how is it produced?
Iron is one of the most widely used and consumed metals in the world. Few structures or factories are found in the world that do not use iron metal or its derivatives. Finished products made from iron have to go through many stages, because first iron ore must be converted to iron and then by combining with different alloys, different types of iron with different chemical compounds and with different degrees of strength as well as different strengths. it is produced. There is a type of iron ore product called sponge iron, which replaces scrap iron and is used to make iron and steel products. In this article, we will first have a definition of sponge iron and then we will explain how to produce sponge iron, advantages and disadvantages, as well as the applications of this product.
What is meant by sponge iron?
When oxygen is removed from iron ore immediately, a spongy iron called porous pellet is produced. The production of sponge iron takes place during the direct reduction of iron or Direct Reduced Iron without melting iron ore. The product of sponge iron, which is in the form of small balls, has a porous appearance and that is why it is called sponge.
After melting, sponge iron is converted into three products during the casting process: ingots, slabs and rebars, which are sent to factories for various uses, where they become other more widely used products. Pellets are high in iron and can be a good substitute for scrap iron. The remarkable thing about pellets is that it refers to sponge iron and is equivalent to it.
Methods of producing sponge iron
Iron ore is generally regenerated by natural gas and coal and leads to the production of sponge iron. The process of reducing iron ore with natural gas is done in three methods, Midrex, HYL and Purofer, of which, Midrex is the most widely used. Also, the process of reducing iron ore and producing sponge iron with coal is done by Jindal DRC and SL / RN methods. In this part of the article, we will explain some of the most widely used methods of producing sponge iron.
Production of sponge iron by Midrex method
This method is one of the best ways to regenerate iron ore. In fact, the production steps of sponge iron are as follows:
First, methane gas enters the refractory unit to decompose into two oxygen-reducing and hydrogen-reducing gases. The decomposed methane is then blown into a cylindrical furnace. As the decomposed methane was blown, iron ore was thrown into the furnace from above to collide with the decomposed methane gas. Decomposed methane natural gas heats up when blown in a furnace, and iron ores lose their oxygen when they come in contact with it. The end product is porous pellets made of pure iron that have been baked and hardened. The sponge iron produced by the Midrex method is more hard and therefore will require more energy during the melting operation.
Production of sponge iron by hyl method
This method also uses natural gas to regenerate iron ore, with the difference that the equipment required and the final product production process is slightly more complex and expensive than the Midrex method. The iron ore reduction process consists of two general parts, namely the natural gas preparation and decomposition part and the iron reduction furnace part. In a natural gas preparation unit, methane natural gas combines with water vapor and decomposes into constituent elements. These elements will then be blown into the furnace with iron ore, the product of which is sponge iron. The sponge iron produced by this process has more carbon in its content and is so-called carburized.
This method is another method of reducing iron ore, which uses coal instead of natural gas for the process. This process consists of a nutrition section where the raw materials are combined. The raw materials include iron ore or iron lumps, which are first introduced into the feeder section, then lime and dolomite along with coal are added to those materials to be sent to a horizontal furnace for the reduction phase. The reason for using dolomite and lime in the composition of raw materials is to help maintain the percentage of sulfur required by the process.
In the horizontal furnace section, which has a very small slope and moves in a circular motion, the raw materials are poured there and move very slowly in that rotary kiln. At this stage, the temperature of the furnace rises so that the coal does not start to burn and starts producing carbon dioxide. The production of carbon dioxide continues until the temperature rises until the iron ore is completely regenerated. The reduced iron ore is then sent to the cooling unit, where it is separated by magnetic methods of sponge iron as the final product.
Sponge iron has the following properties:
Having high amounts of iron and a very high percentage of purity, as well as high metalworking
Its coherence and uniformity in terms of quality
Lack of toxic elements such as lead, tin, zinc, tungsten, etc. in its content
Low content of phosphorus and sulfur in it
Absorbs the least amount of dust along the transport route
Uninterrupted movement in pipes and conveyors due to good and smooth flow
Benefits of sponge iron
Sponge iron and scrap iron are the two raw materials for iron ore and the production of iron and steel products. But sponge iron has more advantages than scrap iron, and therefore most steel mills use it as a raw material. One of the advantages of sponge iron is its purity of iron, which reaches 95%. Therefore, due to the lack of many impurities, it is much easier to use than scrap iron, while this porous pellet is much more economical than other raw materials due to its low energy and water consumption during melting. Another advantage of this raw material is that it has a small amount of nitrogen in its content when it melts, and therefore the products that are produced from it will have better quality.
In addition to the above, sponge iron is easy to store and easy to move and carry; In addition, its use in smelting furnaces eliminates the risk of explosion due to the presence of impurities. Another benefit of this type of iron is its low oxygen consumption during melting. The presence of oxygen in it reduces its resistance, also one of the most important advantages of using this type of porous pellet is not to damage the furnace wall. In addition, the quality of casting products that are produced with this type of iron is very high due to the coherence and lack of toxic elements. Metallurgical operations and smelting are easily performed due to the lack of filtration and consequently the operation of the furnaces will be performed well.
Disadvantages of sponge iron
In addition to its many advantages, sponge iron or porous pellets also have disadvantages. First, the production of sponge iron as a raw material goes through many stages, while scrap iron is sent to a smelter after collection. Another disadvantage of this type of iron is the variety of production stages and finally products with different chemical compositions. In other words, each sponge iron production process produces products with different chemical compositions. Therefore, not all porous pellets are melted at the same temperature.
Application of sponge iron
Porous pellets have found many applications in the manufacture of various types of ferrous products. It is one of the applications of sponge iron in the steel and cast iron industries, which due to the high purity of iron and unique chemical compounds, produces stronger and higher quality steel. Other differences and applications of this type of iron compared to scrap iron are used in the production of weapons and iron tools. In fact, the elements and properties of this iron give the surface more strength to such industries. This type of iron is also used in the manufacture of steel ingots in electric arc furnaces. Making steel ingots with sponge iron greatly increases its productivity and efficiency. It goes without saying that this iron is also used in steel mills as a coolant in LD converters.
Conclusion
Sponge iron is a very important raw material in the manufacture of quality iron and steel products and is therefore used instead of scrap iron. In this article, we tried to introduce sponge iron and its production methods. By introducing its advantages, disadvantages and applications, we were able to get a better view of this raw material. Of course, the use of this type of raw material must be observed in moderation because its main source is iron ore and its extraction may cause damage to the environment.